Recycling is a process that is used in countless industries and is steadily being used more commonly in goods produced today. Recycling is the process of turning waste into usable material. In the packaging industry material is often reused and recycled, which can substantially cut down on the amount of new material and energy that needs to be used to produce more packaging. Three of the most common materials used in the packaging industry are plastic, tin, and aluminium. Studies have shown that recycling aluminum uses 95% less energy than needed to produce new material and recycling plastic saves 76% of the energy [1,2]. This difference is caused by a variety of reasons, like the energy cost to transport, sort, and recycle each product.
The first step in the recycling process is transportation. Materials are picked up from where they have been stored and transported to a recycling facility. This process requires energy, often gasoline, to power the trucks, boats, and railcars that carry the material. The main way to quantify the energy cost of this process is by looking at the amount of trips needed to carry a set amount of material from a starting location to recycling facility. Both tin and aluminium can typically be crushed into a smaller volume than plastic. In addition, the density of aluminium, 2.7 g/cm3, and tin, 7.3 g/cm3, are substantially greater than plastic, 1.5 g/cm3 [3]. This means that by weight more aluminium and tin can be transported in a smaller amount of space than plastic. In the long term this translates to less energy being required to transport tin and aluminium than plastic to a recycling facility [4].
When material reaches a recycling facility one of the first steps is sorting it into groups with similar properties. Both tin and aluminium are relatively easy to sort because they are only separated into a few different groups. Aluminium is separated from other metals using a magnet system. This process uses a large magnet to attract other metals and aluminum remains behind because it is not magnetic [5]. Once the system is in place it requires minimal energy input to maintain. Tin takes more energy to sort, but like aluminium it only has to be separated from all the other metals it is mixed in with. When plastic is recycled it has to be separated by its resin identification code, which is also known as its recycling number. There are seven different recycling codes, which means all plastic is sorted into seven groups. This sorting process can be done in a variety of ways, but typically involves a mix of automated sensors and manual human sorting [6]. This involved process requires substantially more energy input than that of tin and aluminium.
The final step is when the scraps are physically recycled into a new usable material. This process is variable depending on where in the world it is taking place and the facilities available. For both tin and aluminium it is a straightforward process of simply heating the metal until it reaches a molten state. Then impurities are removed, new metals are added if the product is intended to be an alloy, and the metal is cooled. At this point the metal ore is ready to be transported and turned into new packaging. Aluminium and tin can be recycled an infinite number of times and will not lose their properties [7]. For plastic, there are different recycling processes for each of the resin identification codes. Some types of plastic require much more energy than others, but generally they are shredded, heated, chemically treated, and compressed back into a new resin. In terms of overall energy requirements this process is pretty similar to that of recycling tin and aluminum. Both processes use the most amount of energy in the melting stage. Unlike tin and aluminum plastic can only undergo this around 7 times before it begins to lose its properties and must be disposed of [8].
The transport and sorting of tin and aluminium requires substantially less energy than for plastic. The actual recycling process of tin, aluminum, and plastic is relatively similar in energy requirement. When all of this is considered tin and aluminum are clearly the more energy efficient materials to recycle. Recycling one ton of tin or aluminum saves about 14,000 kWh of energy compared to using new materials and recycling one ton of plastic saves about 5,800 kWh of energy [9]. Compared to plastic tin and aluminum have a net savings of close to 8,200 kWh of energy per ton of material recycled. This savings means less fossil fuels have to be burned to produce energy, effectively lessening the amount of CO2 and other greenhouse gasses released into the environment.
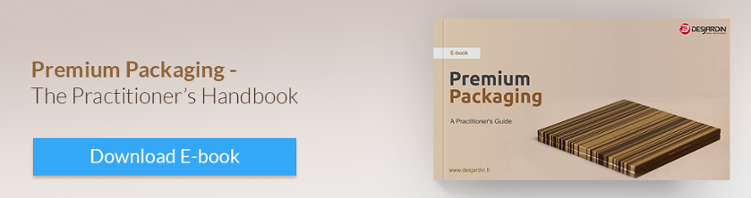
References
[1] "Recycle More NC (archived 2021)"
[2] "Plastics Recycling: Challenges and Opportunities(2009)", by Jefferson Hopewell, Robert Dvorak, and Edward Kosior
[3] "Density elements chart(archived 2021)" ,by Angstrom Sciences
[4] “Aluminum Recycling Economics(2010).” by S.K. Das, J.A.S. Green, and G. Kaufman NATHAN FALDE
[5] "How is Aluminum Recycled: The Recycling Process (2018)" ,by Nathan Falde
[6] "Sorting plastic waste(archived 2021)" , by paprec.com
[7] "Solid Waste from Aluminum Recycling Process: Characterization and Reuse of Its Economically Valuable Constituents(2005)” ,by Shinzato, M.c., and R. Hypolito.
[8] “Life Cycle Assessment of a Plastic Packaging Recycling System(2003)” ,by Umberto Arena, Maria Laura Mastellone & Floriana Perugini
[9] "The Benefits of Aluminum Recycling(2019) ", by Larry West
[10] "Designing a Premium Package: Some Guidelines for Designers and Marketers(2014)", by Ruth Mugge, Thomas Massink ,Erik Jan Hultink Lianne van den Berg-Weitzel